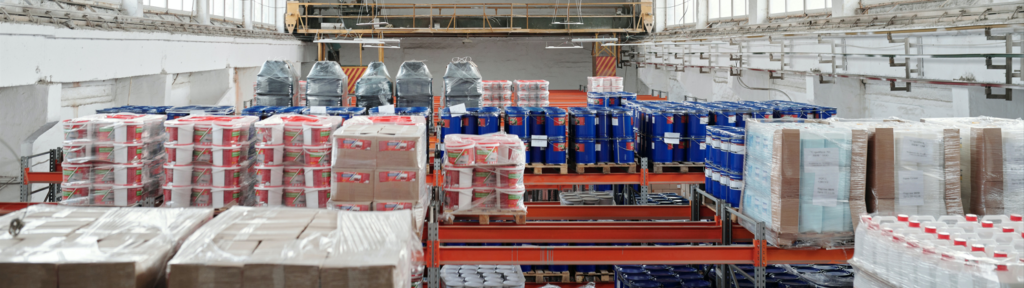
Distribution Quality Services
Lean Biologix is an industry leading consulting firm who has a strong focus on supply chain management and testing for life science manufacturers. Due to this experience Lean Biologix is exceptionally skilled in managing and dealing with distribution-based quality control & quality assurance tasks.
We work with our clients to support and review distribution quality activities in support of their clinical and commercial operations from both the technical and quality assurance perspectives. As a team of consultants, we wear many (“hats”).
We leverage our knowledge of regulatory requirements, industry standards, and best practices to support the distribution quality aspects of shipping qualification for our clients. We bring our expertise and a standardized process for managing shipping qualification programs when assessing distribution quality related items.
Through our proven track record of developing, executing, and reviewing supply chain qualification programs for domestic and international supply chains, we bring a unique side of subject matter expertise to the distribution quality departments we support, allowing for more seamless interaction between Quality Operations and Validation during the process of shipping qualification. Our goal at LBX is to help our clients meet their regulatory and compliance requirements in a timely manner while ensuring we maintain patient safety and product efficacy
How we can help
Supply Chain Lane Assessments
Our team of qualified experts has supported the launch of over 20+ commercial drugs and are capable of overseeing supply chain lane assessments to identify the potential risks, evaluate compliance, and ensure adherence to quality standards. Through this extensive experience, we have learned to identify all potential supply chain risks that can be encountered. Lean Biologix has a proven track record of success and strives to ensure adherence to all quality standards that may potentially affect shipping qualification.
Review of Qualification Reports for
DQ, OQ, and PQ
In shipping qualification, qualification data can often be provided by vendors to support their shipping systems. Lean Biologix has a precise method molded by its long-standing experience of reviewing these vendor provided qualification reports and extrapolating the necessary data to make sure that the suppliers and logistics partners meet the required quality standards set forth in the client’s shipping qualification plan.
Lean Biologix not only has the experience and expertise necessary to design and run a client’s operational and performance qualification testing but also the skills necessary to interpret this data in the event that vendor provided qualification data is not available or adequate. Our skilled engineers are capable of interpolating both thermal and distribution-based qualification testing runs and providing a clear and concise summary of these rounds of testing to ensure that the proposed shippers can maintain product integrity during transportation.
Review of Distribution-Related Documentation
Lean Biologix is uniquely qualified to help potential clients manage distribution-related documentation residing in their document management systems and closely collaborate with their Quality Assurance teams to provide high levels of accuracy and alignment with regulatory and documentation standards. Lean Biologix has frequently integrated into client’s document management systems, so we have a wide host of expertise in different systems making sure we are capable of ensuring accuracy, completeness, and compliance with regulatory requirements in distribution-related documentation.
Driving Continuous Improvement
Lean Biologix always aims to help our clients achieve a higher level of process optimization and efficiency through our experience in industry and our constantly evolving knowledge of new industry best practices. We do this through a combination of our expert knowledge of risk-based approach applications and good distribution/manufacturing processes to constantly provide initiatives within the distribution quality function that identify opportunities for process optimization and efficiency gain.
Risk Assessments
A risk assessment is a process to identify potential hazards and analyze what could happen if a hazard occurs1. Lean Biologix capable engineers have ample experience in considering Business impact analysis and are able to identify compliance risks within the distribution process while also providing mitigations to these potential hazards and have the ability to perform risk assessments to identify and mitigate potential quality and compliance risks within the distribution process.
1.) https://www.ready.gov/risk-assessment/
Periodic Review of Distribution Activities
During a periodic review of the systems, processes, and procedures, they are evaluated to ensure that they have remained in their validated state over the specified time. The purpose of this activity is to identify any changes that may have occurred in the shipping process since the last review and verify that these changes will not negatively impact the process or require additional changes to remain compliant. Lean Biologix is extremely familiar with this process, as many of our clients will keep our teams semi-permanently to conduct the periodic review of their processes.
Quality Agreement (QAG)
Management & Creation
When working with logistics partners for distribution activities, it becomes paramount to have an approved document in place that strictly defines the roles and responsibilities of the logistics partner and the client using them, along with the regulations and stipulations that must be followed by the logistics partner to maintain product quality. Lean Biologix has engineers with contract specialist expertise and a track record of writing QAG documents for clients that make managing the risk of distribution much less of an undertaking.
Deviations, Investigations, and Corrective and Preventive Actions (CAPAs)
Sometimes deviations, investigations, and CAPAs are unavoidable, but with the support of Lean Biologix, these issues can be made more manageable. Through Lean Biologix expert advice and counsel, we aim to support clients through the generation of deviation reports, investigations, and CAPAs related to distribution activities. This support can include execution of newly identified corrective actions and preventive actions, which will result in effective and timely closure of these events in accordance with the client’s quality system regulations (QRS).
Audits & Internal Investigations
Lean Biologix has experience with conducting and resolving both internal and external audits and investigations to ensure compliance with client’s quality requirements. Managing external vendors can be time-consuming between organizing and traveling to suppliers/vendors to generating audit reports. Since the year 2000, Lean Biologix has supported 50+ clients and 20+ successful commercial drug launches. Our expert team knows exactly what regulatory agencies will be looking for and aims to prepare our clients as thoroughly as possible.